Creating things from clay, a bit of water and heat seems magical. You turn a piece of wet, muddy clay into whatever shape you want. The 4 elements working together to produce a dazzling form of art and function.
Pottery is one of the oldest industries in the world and is still in such high demand to this day. As an art form, it mixes science and art to create new and unpredictable pieces.
Pottery can be used for artistic and decorative purposes, such as vases, flowerpots, and urns. It can also be used for functional purposes, such as mugs, bowls, and plates.
Kiln vs. Open Fire
It’s vital to know what to do and what not to do when handling your clay, right from the very first step of shaping it all the way to the final step of firing your pottery. You can use an open fire or an enclosed structure called a kiln.
Using open firing is archaic and somewhat unreliable since there’s no structure within to contain the pottery. It does, however, require a great deal of skill to manage what type of fuel use, as well as being able to control the high temperatures.
Plus, there must be a type of insulation set up to protect you from the flames and extreme heat.
Using a kiln, on the other hand, gives you a better finish. A kiln is simply a huge oven that can reach up to 1500 degrees, and even more. It’s made from rigid, non-melting material so it can withstand the harshness of these extreme temperatures.
It also helps you remain in control of the heat to prevent the pottery piece from breaking or shattering. Kilns usually contain a window, or a ‘spy hole’, to allow you access to check up on your pottery piece.
The Two Stages of Firing
Placing your pottery piece in high temperatures means your piece has reached its most favorable melting point on a molecular level. Firing takes place in two stages.
Bisque Firing
The first stage is known as ‘bisque firing’ which starts at low temperatures with the heat increasing slowly and gradually at a steady pace. This is a crucial part of the firing process to allow all the moisture to leave the piece at an even, constant momentum.
If the temperature rises too quickly or suddenly, the water within the piece will turn to steam, which will cause the piece to shatter.
Once it reaches over 900 degrees, the pottery piece is completely devoid of any moisture.
When you feel the kiln has reached the right temperature for your piece, switch it off and leave it to cool off at its own pace with all the pottery pieces still inside. This gives them the chance to harden even more, without the risk of cracking due to any rapid change in temperature.
Glaze Firing
This second step is what makes your piece waterproof, allowing it to hold liquids, as well as give it extra protection from scratches and scrapes. It’s also the step where you can choose your piece’s color and however way you decide to decorate it.
First off, you have to cover your piece with a layer of glaze, which is then left to dry. Once it has dried, it’s placed once more into the kiln.
You must make sure it’s not touching other pieces. This ensures that they won’t stick together or melt during the glazing process. The kiln is left to slowly reach its desired temperature, then turned off and left to cool slowly once again.
Your piece is finally complete. It’s now a sturdy, waterproof piece of pottery perfection that’ll stand the test of time.
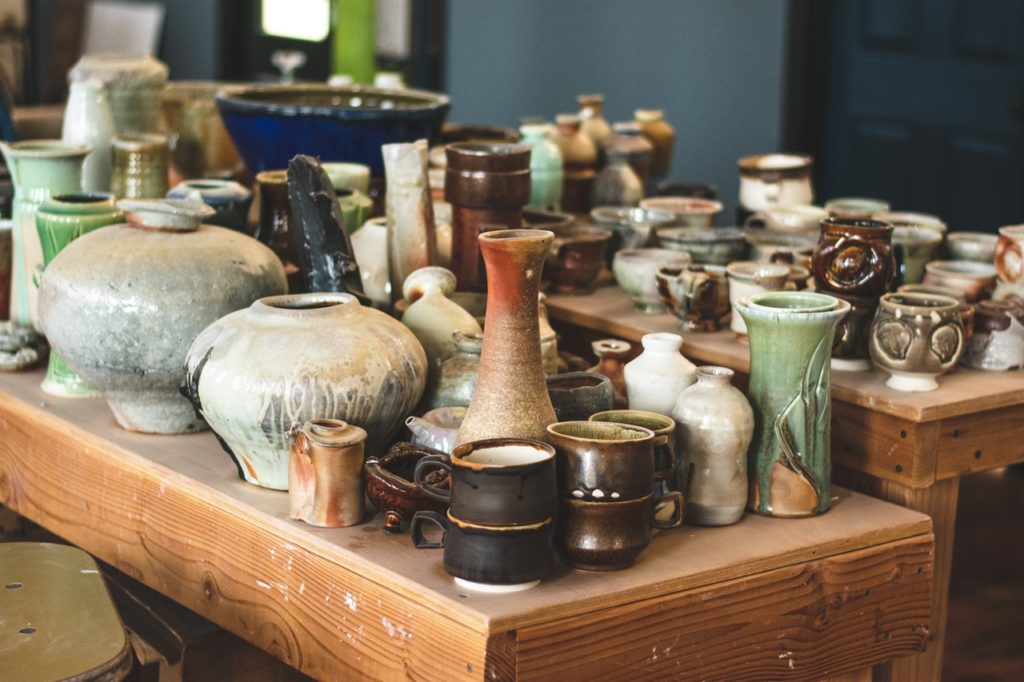
Best Firing Techniques
Each of these firing techniques brings its own design and touch to your pottery. Read on to find out which technique best suits each of your pieces to give them that perfect, sheer finish.
Wood
One of the oldest known firing techniques, wood firing was brought over from Korea to Japan in the 5th century. The wood firing means the kiln gradually reaches very high temperatures by adding in wood at intervals into the bonfire or pit fire.
Wood firing uses wood rather than other types of fuels, such as propane, or gas. This creates ashes and embers, in addition to various minerals from the clay itself, which fall on the surface of the pottery piece creating what’s known as an ‘ash glaze’.
The result varies greatly depending on where each piece is placed in the kiln during wood firing because the flame itself also plays an important part in deciding how it’ll look. Those closest to the fire may be fully submerged in ashes and minerals, while those further away may be less affected.
Pieces made using this firing technique are mainly used for decorative purposes. They aren’t functional and can’t handle the strains and stress of daily use, such as bowls and mugs
Raku
Raku was originally inspired by the ancient Japanese firing method which started in the late 16th century. During this process, the piece was removed from the kiln while the heat is high and bright red. Then it was allowed to cool in the open air.
Nowadays, instead of leaving the piece in the air to dry, it’s placed in a container with a lower temperature. Usually, it’s a container that’s filled with any type of combustible material, such as leaves, newspapers, or sawdust. This step will create a large amount of smoke, so be wary.
Once it’s slightly cooled, it’s dipped into a bin of cold water. This puts a sudden stop to the firing process, creating an assortment of surfaces, such as crackled surfaces, or smokey black unglazed surfaces, or even a lovely metallic surfaces with a sheen finish.
The word ‘raku’ literally means ‘happiness in the accident’ in Japanese. That’s the best way to describe this type of firing technique because it does create some of the most exquisite looking pieces. However, it’s not meant to make functional pieces as other types of firing do. They’re meant to be purely decorative.
Oxidation
During this type of firing, the kiln has a significant amount of oxygen to burn. This process affects the paint colors as well as the glaze itself. They become brighter and richer. It also alters their hue to make them more vibrant than when they first went in.
Oxidation firing is mostly done in an electric kiln but can be done in a gas kiln just the same. It can be done in high or low temperatures.
Reduction
Reduction is the exact opposite of oxidation. It refers to the amount of oxygen entering the kiln being significantly reduced during the firing process.
Typically, this type of firing uses high temperatures. This causes the iron to come up through the pottery piece, creating earthy, warm colors and hues. It also gives a mottled look to the piece, similar to that of a robin’s egg.
This technique refashions the piece’s color and even its visual texture. The reason behind this is that carbon becomes so desperate to find any oxygen.
It dives down into the clay and glaze and plucks out its oxygen molecules. Such a change on the molecular level creates such fascinating designs.
Salt
This type of firing originated in Germany around the 13th century. The trick behind this unpredictable, yet beautiful technique is that salt adheres to the silica found in the clay.
Together, they produce sodium silicate which is glass in its liquid form. So naturally, when sodium silicate sticks to the surface of the piece, it creates a nice, smooth, shiny glaze.
How it’s done is that salt is introduced near the final stages of the bisque firing stage. Baking in a sodium-infused atmosphere gives the pottery piece a glaze-like finish without going through the actual glazing stage.
Occasionally, pieces may come out looking dimply like orange peel, or with a sheen finish. This greatly depends on when the salt is added to the kiln, as well the amount of salt put in.
If the piece isn’t too deep, you can skip the final glaze firing stage. If it’s deep like a mug or a bow, however, it should be glazed since the sodium atmosphere won’t be able to reach down into it.
A Final Note
Whichever piece you decide to create, the final look and feel will mainly depend on the firing technique you choose, along with a few other factors that go into the shape and design of the final product.
The beauty of pottery is that it’s exhilarating and exciting with an infinite number of possibilities to come up with. Its uses are diverse and varied, and it’s techniques are still advancing and growing to this day.