A Brief History of Raku Firing
Raku firing is a unique pottery technique that originated in Japan during the 16th century. It was first developed by the potter Chojiro under the guidance of Zen tea master Sen no Rikyu. The technique was primarily used for creating tea bowls used in the Japanese tea ceremony. Raku, which means “enjoyment” or “ease,” embodies the essence of the Zen philosophy of simplicity and naturalness. Over the years, the Raku technique has evolved and been adopted by potters worldwide, with each artist adding their own unique touch to the process.
The unique appeal of Raku pottery
The Raku firing technique is known for its unpredictable and spontaneous results, making each piece of pottery one-of-a-kind. Raku pottery is characterized by its stunning colors, crackled glaze surfaces, and sometimes smoky, metallic finishes. The process involves quickly heating the pottery in a kiln, removing it while still hot, and placing it into a container with combustible materials. This creates a reduction atmosphere that affects the glazes and clay, producing the distinctive features of Raku pottery. The combination of ancient tradition and modern experimentation make Raku pottery an exciting and rewarding art form for both potters and collectors.
Overview of Raku Firing Technique
Basic principles of Raku firing
Raku firing is centered around three main principles: rapid heating, rapid cooling, and reduction. The process begins with placing the pottery, made from specially formulated Raku clay, into a Raku kiln. The kiln is heated quickly, often reaching temperatures between 1600-1800°F (870-980°C) within an hour or two. Once the desired temperature is reached, the pottery is carefully removed from the kiln using tongs while still glowing hot.
The next step is the reduction phase, where the pottery is placed in a container filled with combustible materials, such as sawdust or leaves. The heat from the pottery ignites the materials, and the container is covered to create a reduced atmosphere. This environment starves the pottery of oxygen and affects the colors and textures of the glazes, leading to the unique Raku finish. After a brief cooling period, the pottery is removed from the reduction container and cleaned to reveal the final result.
Differences from traditional pottery firing
There are several key differences between Raku firing and traditional pottery firing techniques:
- Temperature: Raku firing typically occurs at lower temperatures compared to traditional pottery firing, which can reach 2300-2400°F (1260-1315°C) for stoneware and porcelain.
- Firing duration: Raku firing is much quicker than traditional firing, taking only a few hours from start to finish, while traditional pottery may require a full day or more for firing and cooling.
- Cooling process: In Raku firing, the pottery is rapidly cooled outside the kiln, while traditional pottery is allowed to cool slowly inside the kiln.
- Reduction atmosphere: The reduction phase in Raku firing is responsible for the unique colors and finishes, while traditional pottery typically relies on the kiln atmosphere and glazes alone to produce the final result.
- Fragility: Raku pottery is more porous and fragile than pottery fired using traditional methods, making it primarily decorative rather than functional.
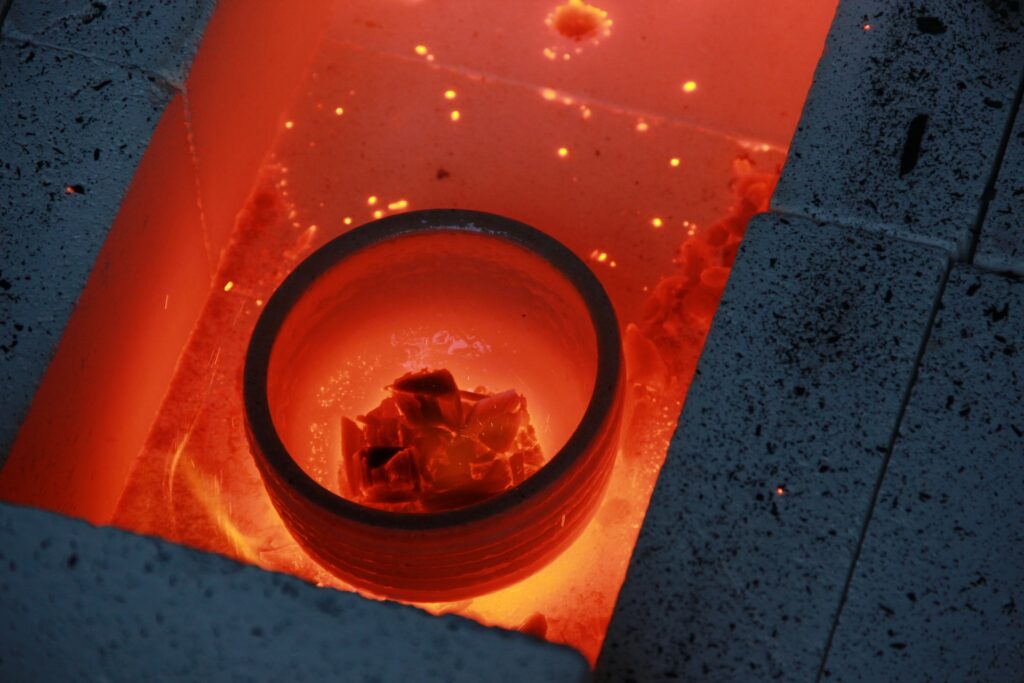
Materials and Equipment Needed for Raku Firing
Raku clay
- Characteristics of Raku clay: Raku clay is specifically formulated for the Raku firing process. It has a high grog content, which is a mixture of pre-fired clay particles. The grog makes Raku clay more resistant to thermal shock, reducing the chances of cracking during the rapid heating and cooling phases. Additionally, Raku clay has a higher percentage of open porosity, making it more suitable for the reduction atmosphere that characterizes Raku firing.
- Where to purchase Raku clay: Raku clay can be purchased at local pottery supply stores, online retailers, or directly from clay manufacturers. Some artists may also choose to mix their own Raku clay using specific clay body recipes.
Raku kiln
- Types of Raku kilns:
- Gas-fired kilns: Gas-fired Raku kilns use propane or natural gas as fuel. They heat up quickly and are easy to control, making them popular for Raku firing. Some gas-fired kilns are designed specifically for Raku, with a top-hat style that allows easy access to the pottery during firing.
- Electric kilns: Electric Raku kilns are less common but can also be used for Raku firing. They require careful temperature control and monitoring, as they tend to heat up more slowly than gas-fired kilns.
- Kiln safety considerations: Safety is crucial when working with Raku kilns. Always follow the manufacturer’s guidelines for operation and maintenance. Keep a fire extinguisher nearby, and ensure the kiln is placed in a well-ventilated area away from flammable materials. Protective clothing, such as heat-resistant gloves and safety goggles, should also be worn during the firing process.
Glazes
- Special Raku glazes: Raku glazes are designed specifically for the Raku firing process. They often contain ingredients that react to the reduction atmosphere, producing a range of vibrant colors and unique surface effects. Some popular Raku glazes include copper matte, crackle, and luster glazes.
- The effects of different glaze formulations: Different Raku glaze formulations will produce various results, depending on the firing temperature, reduction materials, and cooling time. Experimenting with different glaze recipes and firing techniques will help you achieve a wide array of colors, textures, and finishes in your Raku pottery.
Other essential tools and equipment
- Tongs and gloves: Long-handled tongs and heat-resistant gloves are essential for safely removing pottery from the hot kiln during Raku firing. These tools protect your hands from extreme heat and provide a secure grip on the pottery.
- Reduction containers: Reduction containers can be made from metal, ceramic, or other heat-resistant materials. They are used to hold the combustible materials and pottery during the reduction phase of Raku firing. Common container choices include metal trash cans, galvanized steel buckets, and even large ceramic flower pots.
- Safety gear: In addition to heat-resistant gloves, it’s essential to wear other safety gear during Raku firing. This includes safety goggles to protect your eyes from flying debris or intense heat, a face mask or respirator to avoid inhaling harmful fumes, and closed-toe shoes to protect your feet.
The Raku Firing Process
Preparing the pottery
- Shaping and drying: The first step in the Raku process is shaping your pottery from Raku clay. You can use any pottery-making method, such as hand-building or wheel-throwing. Once shaped, the pottery needs to be thoroughly dried before firing. Any moisture left in the clay can turn into steam during firing and cause the pottery to crack or explode.
- Applying the glaze: After the pottery is bone dry, it’s time to apply the glaze. Glazes can be applied by dipping, pouring, or brushing. Always remember to keep the bottom of your pottery free from glaze to prevent it from sticking to the kiln shelf. The glazed pottery should then be left to dry completely before firing.
Firing the pottery
- Loading the kiln: Once your pottery is dry, carefully place it in the kiln. Try to avoid touching the pottery together or with the kiln walls to prevent sticking.
- Monitoring the firing temperature: The kiln is then heated rapidly to the appropriate temperature, usually between 1600-1800°F (870-980°C). An infrared thermometer or pyrometer can be used to monitor the kiln temperature.
- Timing the firing process: Raku firing is relatively fast, typically taking between 30 minutes to an hour to reach peak temperature. The exact timing can vary based on your specific kiln and the size of your pottery.
The reduction phase
- Removing the pottery from the kiln: When the pottery reaches the desired temperature and the glaze has melted, it’s time to remove the pottery from the kiln. Using tongs and wearing heat-resistant gloves, carefully lift each piece from the kiln.
- Placing the pottery in reduction containers: Immediately place the hot pottery into the reduction containers filled with combustible materials. The heat from the pottery will ignite the materials, creating a flame.
- Cooling and cleaning the pottery: Cover the container to create a reduction atmosphere, which starves the pottery of oxygen and influences the final glaze colors. After allowing the pottery to cool in the reduction container for about 15 to 20 minutes, it can be removed and placed in water to cool further. Once the pottery is cooled to room temperature, it can be cleaned using a scrubbing brush to remove any remaining soot or residue and reveal the beautiful Raku effects.
Troubleshooting Common Raku Firing Issues
Cracked or broken pottery
One common issue faced during Raku firing is cracked or broken pottery. This can be due to several factors, such as insufficient drying, trapped moisture in the clay, or uneven heating during firing. To minimize the risk of cracks or breaks, ensure your pottery is completely dry before firing, and avoid using thick or uneven clay walls when shaping your pieces. Using a Raku clay body with a high grog content can also help to reduce the risk of thermal shock and cracking during the rapid heating and cooling process.
Uneven glaze results
Another challenge in Raku firing is achieving even and consistent glaze results. Uneven glazing can result from improper application, contamination of the glaze, or inconsistent firing temperatures. To improve glaze consistency, ensure that your glazes are mixed thoroughly before application and that your pottery is clean before applying the glaze. When firing, maintain an even temperature inside the kiln and allow the glaze to mature fully before removing the pottery. Experimenting with different glaze recipes, firing temperatures, and reduction materials can also help you achieve the desired glaze effects.
Problems with reduction
The reduction phase is a critical part of Raku firing, and issues can arise if this process is not executed correctly. Inadequate reduction can result in dull colors or a lack of luster in your finished pieces. To improve the reduction process, ensure your reduction container is large enough to accommodate your pottery and the combustible materials. Use a generous amount of combustible materials, such as sawdust or leaves, to create a strong reduction atmosphere. Adjusting the timing of the reduction phase and experimenting with different materials can also help you achieve better results. Remember that Raku firing is an inherently unpredictable process, and some variation in results is to be expected.
Inspirational Raku Pottery Artists
Traditional Japanese Raku masters
The Raku pottery technique originated in Japan, and there are several traditional Japanese Raku masters who have made significant contributions to the art form. Chojiro, the first-generation Raku master, is credited with developing the Raku technique in the 16th century under the guidance of tea master Sen no Rikyu. Chojiro’s descendants, who continue to create Raku pottery today, have preserved and refined the technique through the generations. Some notable traditional Raku masters include:
- Chojiro – The founder of the Raku tradition and creator of the first Raku tea bowls.
- Raku Kichizaemon – The current and 15th generation Raku master, who continues the family tradition by creating unique and contemporary Raku pottery while honoring its rich history.
Contemporary Raku artists
In addition to traditional Japanese Raku masters, many contemporary Raku artists from around the world have embraced and expanded upon the technique. These artists bring their unique perspectives and creativity to Raku pottery, experimenting with new glaze formulations, firing techniques, and artistic styles. Some noteworthy contemporary Raku artists include:
- Paul Soldner – An American artist who revolutionized Raku in the West, developing the American Raku technique, which incorporates post-firing reduction and emphasizes individual expression.
- Steven Branfman – An American potter and educator known for his distinctive Raku pottery and extensive written works on Raku ceramics.
- Kate Malone – A British ceramic artist who creates intricately designed Raku pottery inspired by nature, with striking textures and vibrant glaze effects.
- David Roberts – An English artist recognized for his large-scale Raku ceramics, which combine traditional Raku techniques with innovative sculptural forms.
Tips for Beginners in Raku Firing
Embracing the unpredictable nature of Raku
One of the most important tips for beginners in Raku firing is to embrace the unpredictable nature of the process. Raku pottery is known for its unique and varied results, which are influenced by many factors, such as the type of clay, glaze formulation, firing temperature, and reduction materials. Beginners should be open to surprises and learn to appreciate the unexpected beauty that can emerge from the Raku process. Understanding that not every piece will turn out as planned can help reduce frustration and encourage artistic growth.
Experimenting with different glazes and firing techniques
Experimentation is key to success in Raku pottery. Beginners should not be afraid to try different glaze recipes, firing temperatures, and reduction materials to discover the effects they produce. This process of experimentation can lead to new and exciting discoveries, helping you develop your unique style and refine your technique. Taking notes and documenting your process can be helpful for tracking your progress and replicating successful results in the future.
Taking safety precautions
Raku firing involves working with high temperatures, open flames, and potentially harmful fumes, making safety a top priority. Beginners should familiarize themselves with the necessary safety precautions before starting the Raku process. This includes wearing heat-resistant gloves, safety goggles, and closed-toe shoes; working in a well-ventilated area; and having a fire extinguisher on hand. Additionally, it is crucial to follow the manufacturer’s guidelines for kiln operation and maintenance to ensure a safe and successful Raku firing experience.
Conclusion
The beauty and appeal of Raku pottery
Raku pottery is known for its unique beauty, with captivating glaze effects, vibrant colors, and unpredictable results. The rapid firing and reduction process lends itself to the creation of one-of-a-kind pieces that embody the fusion of art, skill, and chance. The history and tradition of Raku pottery, combined with the opportunity for personal expression and experimentation, make it an alluring and rewarding art form for both experienced potters and beginners alike.
For those interested in trying Raku firing, remember that the journey is as important as the destination. Embrace the unpredictable nature of Raku and be open to the learning process. Experiment with different techniques, glazes, and materials to develop your unique style, and don’t forget to prioritize safety throughout your creative endeavors. Raku firing can be an immensely satisfying and enjoyable experience, providing a platform for artistic growth, personal expression, and the creation of truly remarkable pottery.